EXPLAINED: Carbon dioxide liquefaction and purification
April 19, 2021
CCS is a climate engineering initiative.
It’s necessary to liquefy carbon dioxide to enable and maintain a flexible transportation network between the various carbon dioxide sources and the storage sites. The process design of a liquefaction unit depends on several prerequisites such as chosen carbon capture technology, carbon dioxide specifications and facility location.
The liquefaction process consists of a number of combined compression, purification and cooling steps. The process can be divided into two categories based on the choice of cooling method:
- Liquefaction by low-pressure cooling with external refrigerants
- Direct compression of gas and internal cooling by expansion and re-circulation of liquefied carbon dioxide
On the first figure you’ll see a schematic process model for low-pressure liquefaction using ammonia as a refigerant. The ammonia is recovered in a separate process loop where it is compressed, cooled and reused. In order to separate non-condensable gases, such as oxygen, the liquefied carbon dioxide is heated using a reboiler. Carbon dioxide off gas could also be recovered throughout the process.
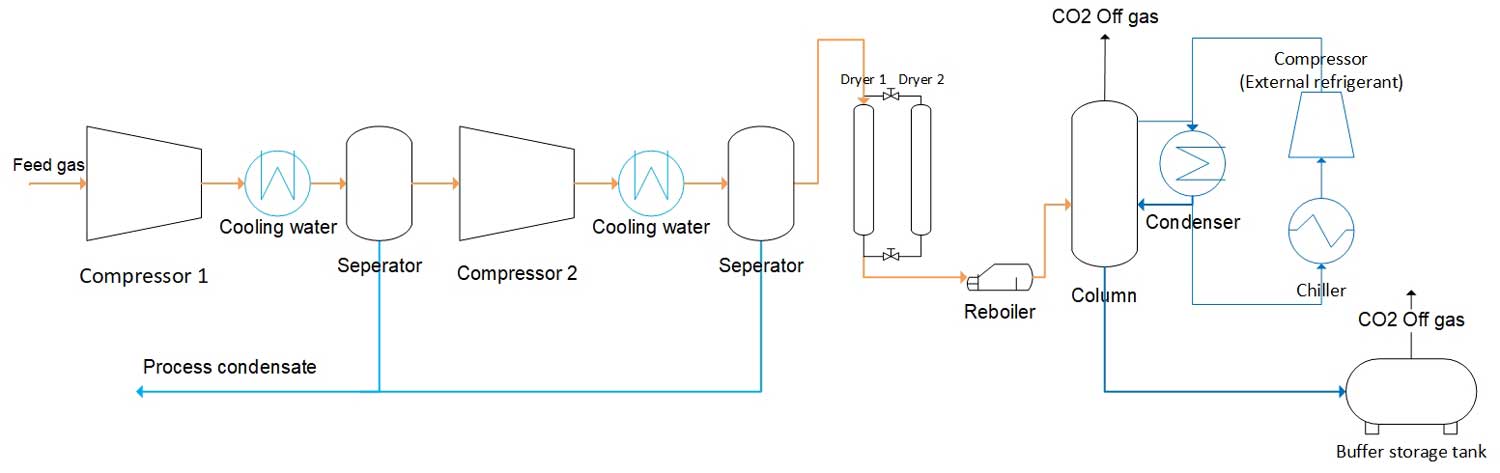
Liquefaction by internal cooling allows the carbon dioxide gas to expand resulting in a drop in temperature which is describe by the Joule-Thomson effect. The gas is compressed to a higher pressure than transport specification before entering the condenser. Non-liquefied carbon dioxide is recycled to the previous cooling step and used as a refrigerant.
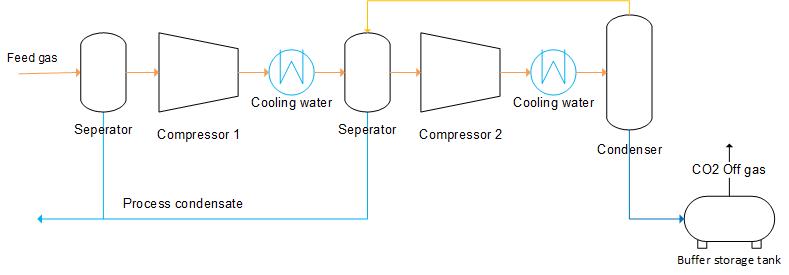
We help our customers to establish the best process setup based on their local conditions. We offer impartial and fact-based Heat & Mass calculations as well as Capex, Opex and Footprint estimations. Please contact us for more information.